- 08/09/2023
- Posted by: Thamizharasu Gopalsamy
- Categories: Management, Manufacturing
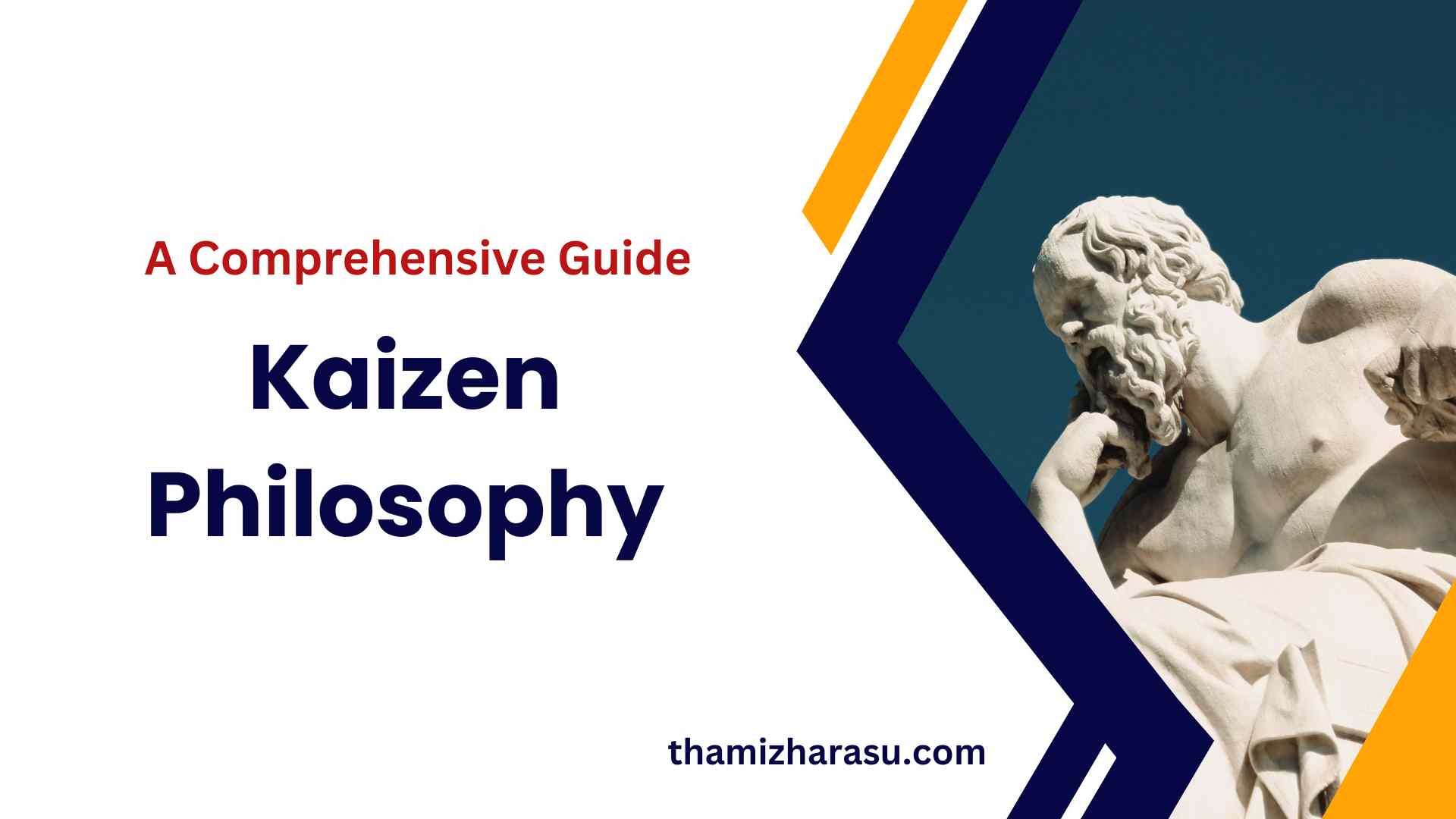
Introduction:
In a world that’s perpetually changing, the quest for improvement never ends—be it in business, personal development, or even societal growth. The Kaizen Philosophy, originating from Japan, offers a powerful framework for continual improvement. From its historical roots to modern applications in diverse sectors, this comprehensive guide aims to help you grasp the essence of Kaizen and its transformative power.
Kaizen Philosophy Explainer Video
1. Introduction to the Kaizen Philosophy: What You Need to Know
In a rapidly evolving world, the ability to adapt and improve is more vital than ever. This is where the Kaizen philosophy comes into play. Originating from Japan, the term ‘Kaizen’ is a fusion of two words: ‘Kai,’ which means change, and ‘Zen,’ which means good. Together, they signify change for the better or continuous improvement.
What is the Kaizen Philosophy?
The Kaizen philosophy is a time-tested approach that focuses on making small, incremental changes to improve productivity, quality, and effectiveness across various aspects of life—be it in manufacturing, business processes, or even personal development. Unlike drastic changes that can cause disruption, Kaizen aims for long-term, sustainable improvement through continuous efforts.
Why is Kaizen Important for Businesses?
1. CostEfficiency: By improving processes incrementally, businesses can reduce waste and optimize resources without incurring huge costs.
2. Employee Engagement: Kaizen encourages a culture where every employee, from the janitor to the CEO, is encouraged to suggest improvements. This not only empowers employees but also fosters a sense of ownership and teamwork.
3. Customer Satisfaction: Consistent improvement in quality and services naturally leads to higher customer satisfaction and loyalty.
4. Scalability: Because Kaizen focuses on small changes, it’s easier to test, iterate, and implement new processes, making it ideal for businesses of all sizes.
Why is Kaizen Relevant for Individuals?
While often associated with businesses and manufacturing, the principles of Kaizen can be applied in everyday life as well. From learning a new skill to improving your health, the Kaizen philosophy can help you reach your goals in a manageable, less intimidating manner. For instance, reading just five pages of a book each day or dedicating 10 minutes daily to a new hobby can result in significant improvement over time.
Conclusion: Understanding the Kaizen philosophy is the first step towards embracing a culture of continuous improvement, both personally and professionally. Whether you are a business owner looking to streamline operations or an individual aspiring to personal growth, Kaizen offers a structured approach to achieving your objectives.
2. The Origins of Kaizen Philosophy: A Historical Perspective
Understanding the roots of the Kaizen philosophy requires us to journey back to post-World War II Japan. As the country faced the daunting task of rebuilding its economy, a new approach to industrial management emerged, built around the philosophy of continuous improvement or ‘Kaizen.’
Ancient Origins in Japanese Culture
Although popularized in the mid-twentieth century, the tenets of Kaizen can be traced back to traditional Japanese culture, where the spirit of constant improvement is deeply embedded. Whether it was the meticulous artistry of tea ceremonies or the discipline involved in martial arts, the essence of Kaizen was always present.
American Influence on Modern Kaizen
Interestingly, Kaizen as we know it today was heavily influenced by American business management theories, particularly Total Quality Management (TQM) and JustInTime (JIT) production. American experts like W. Edwards Deming and Joseph M. Juran were instrumental in shaping Japan’s industrial landscape, indirectly contributing to the formalization of the Kaizen philosophy.
Kaizen and the Toyota Production System
One of the most well-known applications of Kaizen comes from Toyota Motor Corporation, where it became an integral part of the Toyota Production System. It allowed Toyota to produce high-quality cars more efficiently and with less waste, becoming a global standard for manufacturing excellence.
Kaizen in the Western World
After proving its effectiveness in Japan, Kaizen began to gain international recognition. Companies in the U.S., Europe, and beyond started to adopt the philosophy in various sectors, from healthcare to software development. While the application varied, the core principle remained the same: incremental improvements lead to substantial gains over time.
The Evolution of Kaizen
Over the decades, Kaizen has evolved to include various tools and methodologies, such as Six Sigma, Lean Management, and the 5S system. Its core principles have been adapted to suit the unique needs of different industries and have even found relevance in personal development and psychology.
Conclusion: The Kaizen philosophy, though rooted in Japanese culture, has universal applicability. Its time-tested approach has been instrumental in shaping not just businesses but also individual lives, reaffirming the power of continuous improvement. As we move into an increasingly competitive and complex world, the history of Kaizen serves as a potent reminder that small, sustained changes can yield significant results.
3. Kaizen Philosophy in Business: Boosting Efficiency and Productivity
In a business landscape characterized by competition and rapid changes, organizations that stand still risk becoming obsolete. This is where the Kaizen philosophy shines. By adopting a culture of continuous improvement, businesses can not only sustain but excel in today’s market. Here’s how the Kaizen philosophy can boost efficiency and productivity in your business.
Operational Excellence through Incremental Changes
While it’s tempting to look for grandiose, quick fixes to operational issues, Kaizen focuses on making small, consistent improvements. These minor adjustments, when aggregated, can lead to a significant enhancement in the quality and speed of business operations.
Empowering the Workforce
One of the core principles of Kaizen is involving everyone in the improvement process. Employees at all levels are encouraged to make suggestions, no matter how minor they may seem. This democratic approach enhances job satisfaction, boosts morale, and contributes to a more engaged, productive workforce.
Improving Customer Satisfaction
The Kaizen philosophy isn’t just inward-focused; it has a direct impact on customer satisfaction. By continually improving the quality of products or services, businesses can meet customer expectations more effectively, thereby boosting customer retention rates.
Streamlining Supply Chain Management
In a complex supply chain, inefficiencies can often go unnoticed. Kaizen’s philosophy emphasizes consistent monitoring and iterative improvement, thereby minimizing waste and optimizing supply chain operations.
Enhanced Resource Utilization
Kaizen helps identify redundancies and areas where resources are underutilized. By reallocating these resources efficiently, companies can maximize their output without additional financial burden.
Risk Management and Compliance
Through its methodical approach to process improvement, Kaizen can also aid in identifying potential areas of risk and noncompliance. Businesses can thus proactively address these issues before they escalate into costly problems.
Lean Management and Kaizen
Lean management, which emphasizes reducing waste and optimizing workflows, dovetails perfectly with Kaizen. The synergy between these two approaches can result in substantial gains in efficiency and profitability.
Metrics and KPIs: Tracking Success
It’s vital to track the effects of implementing the Kaizen philosophy. Key Performance Indicators (KPIs) like process times, defect rates, and employee engagement levels can offer invaluable insights into the success of your Kaizen initiatives.
Conclusion: The Kaizen philosophy offers a proven, practical framework for achieving higher levels of efficiency and productivity in the business arena. By ingraining the culture of continuous improvement into your organization, you set the stage for sustained growth and long-term success.
4. The Five Pillars of Kaizen Philosophy
At its core, Kaizen is more than just a methodology for process improvement; it’s a philosophy that influences every aspect of life. To fully comprehend the power of Kaizen, it’s essential to explore its five pillars that form the backbone of this approach.
1. Teamwork
What it means: Kaizen places a strong emphasis on collective responsibility and teamwork.
Why it matters: In a team setting, the diverse strengths and perspectives of each member can contribute to more robust and effective solutions.
How to apply it: Encourage group discussions, workshops, and collaborative projects that foster a sense of unity and shared goals.
2. Personal Discipline
What it means: This pillar refers to an individual’s commitment to reliably follow established rules and procedures.
Why it matters: Without personal discipline, even the most well-planned processes and guidelines become ineffective.
How to apply it: Promote a culture that values punctuality, responsibility, and meticulousness in everyday tasks.
3. Improved Morale
What it means: Kaizen encourages a positive work environment and mental attitude.
Why it matters: Higher morale leads to increased productivity, reduced turnover, and improved overall well-being for everyone involved.
How to apply it: Celebrate small victories, recognize individual and team contributions, and create a supportive work environment.
4. Quality Circles
What it means: These are small groups that perform quality checks and brainstorm ways to improve methods, products, or services.
Why it matters: Constant quality checks and discussions help to identify areas of improvement that might otherwise go unnoticed.
How to apply it: Implement regular meetings where team members can discuss quality control and suggest improvements.
5. Suggestions for Improvement
What it means: Kaizen thrives on continuous improvement, and that often starts with suggestions from team members.
Why it matters: Fresh perspectives and new ideas are the lifeblood of innovation and progress.
How to apply it: Create an open channel for employees to submit their suggestions and make it a point to review and implement viable ideas.
Conclusion: The five pillars of Kaizen philosophy—Teamwork, Personal Discipline, Improved Morale, Quality Circles, and Suggestions for Improvement—work in harmony to create a culture of continuous growth and development. By understanding and applying these principles, both businesses and individuals can set themselves on a path toward sustained success.
5. How to Implement Kaizen Philosophy in Small Businesses
While Kaizen has its roots in large manufacturing settings, its principles are incredibly adaptable and can bring significant benefits to small businesses as well. The inherent advantage for smaller organizations lies in their flexibility and the ease with which they can implement changes. Below are some practical tips to integrate the Kaizen philosophy into small business operations.
1. Begin with Training
What to do: Conduct training sessions to familiarize your team with the Kaizen philosophy.
Why it matters: Proper understanding is the first step toward effective implementation.
How to go about it: Use online resources, and workshops, or even bring in a consultant for an intensive, hands-on training session.
2. Set Clear Objectives
What to do: Define what you aim to achieve with Kaizen—be it reducing waste, improving customer satisfaction, or boosting sales.
Why it matters: Goals serve as a roadmap and provide motivation.
How to go about it: Set SMART goals (Specific, Measurable, Achievable, Relevant, Timebound) to make objectives clear and quantifiable.
3. Involve Everyone
What to do: Ensure that every member, from the manager to the janitor, is involved in the Kaizen process.
Why it matters: Solutions can come from anywhere, and involving everyone ensures a wider range of perspectives.
How to go about it: Create an open platform where everyone can submit their suggestions for improvement.
4. Start Small
What to do: Begin by identifying minor issues that can be easily fixed.
Why it matters: Small successes build momentum and make tackling bigger problems easier.
How to go about it: Focus on one department or a single process and expand from there.
5. Use Kaizen Tools
What to do: Utilize tools like the PDCA cycle (PlanDoCheckAct) and 5 Whys for problem-solving and continuous improvement.
Why it matters: These tools provide structured approaches to identify issues and find solutions.
How to go about it: Use these tools in team meetings to dissect problems and brainstorm solutions.
6. Monitor and Review
What to do: Regularly track your progress against the set objectives.
Why it matters: Monitoring helps you understand the impact of your efforts and make necessary adjustments.
How to go about it: Use Key Performance Indicators (KPIs) to measure success and hold periodic reviews.
7. Celebrate and Iterate
What to do: Celebrate your successes, no matter how small, and use them as stepping stones for future improvements.
Why it matters: Celebrations boost morale and create a culture that values progress.
How to go about it: Share success stories, give small rewards, and continually iterate based on what you’ve learned.
Conclusion: Implementing the Kaizen philosophy in a small business setting might seem daunting, but by taking a structured, step-by-step approach, it becomes not just manageable but highly rewarding. With Kaizen, the size of your business doesn’t matter; it’s the size of your commitment to improvement that truly counts.
6. Kaizen in Manufacturing: A Case Study
One of the sectors where the Kaizen philosophy has been most impactful is manufacturing. Real-world examples offer invaluable insights into how these principles can be applied to create a more efficient, productive, and profitable operation. Let’s dive into a case study featuring ‘XYZ Manufacturing Co.,’ a midsized automobile parts manufacturer.
The Challenge
XYZ Manufacturing Co. was facing stagnation in productivity levels, resulting in delayed orders and growing operational costs. With competitors providing similar quality at a lower price point, the company was losing market share.
Initial Assessment
On conducting an initial assessment, the company found several areas where inefficiencies existed, ranging from equipment downtime to excess inventory. To overcome these challenges, XYZ decided to implement the Kaizen philosophy.
The Kaizen Approach
1. Training and Orientation: All employees were trained on Kaizen principles and the benefits they could bring to their specific roles.
2. Gemba Walks: Management conducted regular ‘Gemba Walks’—a practice where leaders observe the work process—to identify bottlenecks.
3. Suggestion Boxes: An open suggestion system was installed, encouraging employees to contribute ideas for improvement.
Key Changes and Results
1. Reduced Equipment Downtime: Through regular inspections and predictive maintenance, equipment downtime was reduced by 30%.
2. Optimized Inventory: JustInTime inventory methods were adopted, cutting storage costs by 20%.
3. Improved Quality: Quality Circles led to a 15% reduction in product defects, enhancing customer satisfaction.
4. Employee Satisfaction: The open suggestion system led to the implementation of 50 new improvements, resulting in increased employee satisfaction and reduced turnover.
Metrics for Success
30% increase in overall productivity
20% reduction in operational costs
15% higher customer satisfaction rates
Conclusion: The case study of XYZ Manufacturing Co. serves as an excellent example of how the Kaizen philosophy can revolutionize manufacturing processes. It shows that the principles of Kaizen are not just theoretical constructs but practical tools that can bring about transformative changes.
7. Benefits of Adopting Kaizen Philosophy in Service Industries
While the Kaizen philosophy originated in the manufacturing sector, its principles are universal and can offer substantial benefits to service-oriented industries as well. From healthcare to hospitality and IT services, the scope for implementing Kaizen is vast. Let’s delve into the multiple advantages of adopting this philosophy in service industries.
1. Enhanced Customer Experience
What it means: Applying Kaizen principles can lead to improved service quality and customer interactions.
Why it matters: In a service industry, customer satisfaction is the ultimate metric of success.
How it works: Regular feedback loops with customers can identify pain points, allowing for incremental improvements that lead to enhanced customer satisfaction.
2. Process Streamlining
What it means: Kaizen helps in identifying redundancies and bottlenecks in service delivery.
Why it matters: Streamlining processes can dramatically reduce service delivery time and cost.
How it works: Tools like flowcharts and process mapping can make inefficiencies glaringly obvious, providing clear targets for improvement.
3. Employee Engagement
What it means: Kaizen involves all employees in the continuous improvement process.
Why it matters: Engaged employees are more productive and contribute to a healthier work environment.
How it works: Programs like suggestion boxes or regular team huddles can help gather ideas from all staff members, making them feel valued and engaged.
4. Cost Efficiency
What it means: Kaizen principles help identify waste in the form of time, resources, or material.
Why it matters: Reducing waste translates directly to cost savings.
How it works: Regular audits and reviews can help pinpoint areas where resources are being underutilized or wasted.
5. Scalability
What it means: Effective implementation of Kaizen can make scaling your business easier.
Why it matters: A streamlined, efficient process is easier to replicate across multiple locations or departments.
How it works: Standardized processes and best practices can be uniformly implemented, making scaling less chaotic and more effective.
6. Innovation
What it means: A culture of continuous improvement fosters innovation.
Why it matters: In the fast-paced world of service industries, innovation is key to staying ahead of fast-paced.
How it works: Encouraging employees to think creatively and offer suggestions creates an environment ripe for innovative solutions.
Conclusion: From improving customer satisfaction to engaging employees and cutting costs, the benefits of implementing Kaizen in service industries are manifold. It provides a structured yet flexible framework that can adapt to the unique challenges and opportunities present in service-oriented businesses.
8. Kaizen Philosophy and Personal Development: A Comprehensive Guide
The Kaizen philosophy is not confined to the corporate world; its principles can be wonderfully applied to personal development as well. Just as continuous improvement can lead to business success, adopting Kaizen can help you achieve your personal goals. Here is a comprehensive guide on how you can use Kaizen for self-improvement.
1. Understanding the Self: The First Step
What it means: Just as a business would assess its operations, self-assessment is the cornerstone of personal development.
How it works: Use self-assessment tools or reflection techniques to understand your strengths, weaknesses, opportunities, and threats (SWOT).
2. Setting Realistic Goals
What it means: Aim for achievable, specific, and time-bound goals.
How it works: Break down large goals into smaller, manageable tasks and set deadlines.
3. Daily Improvement
What it means: Adopt the Kaizen approach of making small daily improvements.
How it works: Instead of trying to make radical changes overnight, focus on 1% improvements each day in areas like learning, fitness, or productivity.
4. Eliminating Waste
What it means: Identify and remove wasteful habits or distractions that impede your growth.
How it works: Use time tracking tools to monitor how you spend your time and identify timewasters.
5. Learning from Mistakes
What it means: Embrace failures and mistakes as learning opportunities.
How it works: Adopt a growth mindset that sees challenges as opportunities for improvement.
6. The Feedback Loop
What it means: Continuously seek feedback to make course corrections.
How it works: Use regular self-evaluation or seek feedback from mentors, peers, or family members.
7. Kaizen and Mindfulness
What it means: The practice of mindfulness can complement Kaizen by enhancing self-awareness.
How it works: Mindfulness can help you become aware of your thoughts and actions, making it easier to instigate change.
8. The Role of Habit
What it means: Consistent habits form the backbone of sustained personal development.
How it works: Use habit-tracking apps or techniques like the Habit Loop to establish new positive routines.
9. Community and Kaizen
What it means: Community support can amplify your efforts.
How it works: Engage with like-minded people in forums or support groups who can hold you accountable for your goals.
10. Measuring Success
What it means: Set metrics to gauge your progress.
How it works: Use apps or journaling to track your progress, be it in weight loss, skill acquisition, or financial goals.
Conclusion: The principles of Kaizen philosophy offer a robust framework for personal development. By adopting the Kaizen mindset, you can bring about gradual but impactful changes that cumulate into significant personal growth over time.
9. Kaizen Tools and Techniques: Your Ultimate Guide
The effectiveness of the Kaizen philosophy lies not just in its principles but also in the tools and techniques that facilitate its implementation. These range from simple organizational tools to more complex analytical frameworks. This ultimate guide aims to familiarize you with some of the essential Kaizen tools and techniques.
1. Gemba Walks
What it is: A practice where managers visit the workplace to observe processes.
How it helps: Identifies bottlenecks and inefficiencies directly, enhancing decision-making.
2. The 5 Whys Technique
What it is: Asking Why? five times to drill down into the root cause of a problem.
How it helps: Eliminates symptoms and focuses on the core issue, enabling effective solutions.
3. PDCA Cycle (PlanDoCheckAct)
What it is: A repetitive four-stage model for continuous improvement.
How it helps: Facilitates a structured approach for problem-solving and implementing changes.
4. Value Stream Mapping
What it is: A flowchart that visualizes the steps needed to take a product from start to finish.
How it helps: Helps in identifying waste and streamlining processes.
5. Kanban System
What it is: A visual tool that helps in managing workflow and operational aspects.
How it helps: Increases visibility into the status of tasks and projects, promoting efficiency.
6. Kaizen Blitz
What it is: A focused, short-term project to improve a specific area or process.
How it helps: Achieves quick, significant improvements in a limited timeframe.
7. Standard Work
What it is: Documentation of the best practices for each process.
How it helps: Ensures consistency and helps in training new employees.
8. Heijunka (Production Leveling)
What it is: Balancing workload to minimize fluctuations and waste.
How it helps: Improves efficiency by making production more predictable.
9. Takt Time
What it is: The rate at which products must be produced to meet customer demand.
How it helps: Ensures that production aligns with actual demand, reducing waste.
10. Andon
What it is: A visual alert system to signal problems in real-time.
How it helps: Enables immediate corrective actions, reducing downtime and waste.
Conclusion: Understanding and effectively utilizing these tools and techniques can significantly impact the successful implementation of the Kaizen philosophy in your organization. From simple techniques like the 5 Whys to more complex methodologies like Value Stream Mapping, each tool has its unique advantage in the Kaizen ecosystem.
10. Measuring the Impact of Kaizen Philosophy in Your Organization
The journey through the Kaizen Philosophy is not just a one-time endeavor but a continuous process that seeks incremental improvements in various facets of business and personal development. But how do you know if Kaizen is working? Measuring its impact is crucial to ensure that your efforts are paying off.
Key Takeaways
1. Versatility: Kaizen is adaptable to different sectors, from manufacturing to services, and can even be applied to personal development.
2. Employee Engagement: Kaizen fosters a culture where every team member feels empowered to suggest improvements.
3. Sustainability: The focus is on long-term, sustainable changes rather than quick fixes.
4. CostEffectiveness: By targeting waste and inefficiencies, Kaizen often leads to significant cost savings.
5. Innovation: A Kaizen culture is an innovative culture, as employees are encouraged to think critically and propose solutions.
Metrics for Measuring Kaizen Effectiveness
1. Customer Satisfaction Scores: These can indicate how well your improvements are translating into customer satisfaction.
2. Employee Engagement Levels: Surveys or interviews can help gauge the degree of employee participation and satisfaction.
3. Operational Metrics: Key Performance Indicators (KPIs) like delivery times, defect rates, and productivity levels can offer quantitative insights.
4. Financial Metrics: Return on Investment (ROI) for specific Kaizen initiatives can be a direct measure of success.
5. Benchmarking: Comparing your performance metrics with industry standards can provide an external perspective on your achievements.
Next Steps
1. Regular Reviews: Keep track of the metrics to ensure you’re moving in the right direction.
2. Feedback Loops: Create mechanisms for regular feedback from both employees and customers.
3. Celebrate Wins: Acknowledge and celebrate even small successes to keep the momentum going.
Final Thoughts
Adopting the Kaizen Philosophy is more than just implementing a set of tools or techniques; it’s about changing the very fabric of your organizational culture to one that seeks continuous improvement. By understanding the key principles, leveraging the right tools, and most importantly, measuring your results, you can achieve sustainable growth and success.
Conclusion:
Adopting the Kaizen Philosophy isn’t just a procedural change; it’s a cultural shift that drives continuous improvement in every facet of life. As we have explored through its principles, applications, and tools, Kaizen fosters not only business efficiency but also personal growth. Measuring its effectiveness through various metrics ensures that you are on the right track toward sustainable success. Embrace Kaizen today and unlock the potential for limitless improvement.
Would you like to improve your systems and processes in your businesses? For free consultation submit the form below.